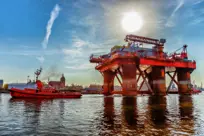
Erfahren Sie mehr über Anstrichsysteme
Elektromotoren, Getriebe und andere Metallbauteile, die unter rauen Umweltbelastungen eingesetzt werden, erfordern manchmal einen zusätzlichen Schutz. Die entsprechenden Schutzbeschichtungen verlängern die Lebensdauer und senken das Korrosionsrisiko.
Salz, chemische Mittel, Feuchtigkeit und Verschmutzungen – dies sind nur einige der Faktoren, die eine Beeinträchtigung von Metallteilen bewirken. Die unter ungünstigen Umweltbelastungen arbeitenden Maschinen erfordern spezielle Korrosionsschutzbeschichtungen. Eine Pumpe, die ständiger Feuchtigkeit ausgesetzt ist, ein Motor auf der Spitze einer Windkraftanlage oder ein Kran auf einer Bohrplattform sind nur einige Beispiele.
Die richtige Wahl
Oftmals ist die Schutzklasse festgelegt und die eingesetzte Applikation muss mit den vorgegebenen Anforderungen übereinstimmen. Die Schutzklasse betrifft die gesamte Konstruktion und hängt von solchen Parametern, wie der Art des Metalls, der Oberflächenstruktur und der Wartungsintervalle ab. Bei jeglichem Zweifel in Bezug auf die geforderte Beschichtung und der Oberflächenbehandlung sollte immer ein Experte konsultiert oder Informationen beim Endanwender eingeholt werden.
Klassifizierung C und NORSOK M501
Die am häufigsten eingesetzte Norm, die bei der Bestimmung des Schutzgrades einer Oberflächenbehandlung eingesetzt wird, ist ISO 12944. Sie wurde speziell für die Berechnung des Korrosionsgrades für große Stahlkonstruktionen, die dem Einwirken äußerer Faktoren ausgesetzt sind, erstellt. Die Norm NORSOK M501 wurde aus ähnlichen Gründen von der norwegischen petrochemischen Industrie erstellt.
Beide Normen beziehen sich auf die flache Metalloberfläche und nicht auf Elemente mit komplizierter Geometrie, wie Motoren oder Kräne. Deshalb kann der entsprechende Schutzgrad auch nur annähernd bestimmt werden.
ISO 12944 legt fünf Hauptklassifizierungen von Korrosion auf einer Skala von C1 bis C5 fest. Für Umgebungen mit C3 und höher wird in der Regel eine zusätzliche Oberflächenbehandlung gefordert. Dies hängt jedoch vom Standardanstrich und der gegebenen Anwendung ab.
Kategorien des Korrosionsgrades | Verwendung im Freien | Verwendung in Innenräumen |
C1 – sehr niedrig | – | Beheizte Gebäude mit sauberer Luft, zum Beispiel Büros, Schulen oder Hotels. |
C2 – niedrig | Schadstoffarme Atmosphäre, typisch ländliche Umgebung. | Unbeheizte Gebäude mit Kondensationsgefahr, wie z. B. Lagerhallen. |
C3 – mittel | Städtische oder industrielle Umgebungen, mäßige Schwefeldioxidbelastung, Küstengebiete mit niedrigem Salzgehalt. | Fabrikgebäude mit hoher Luftfeuchtigkeit und Luftverschmutzung, z. B. in der Lebensmittelproduktion. |
C4 – hoch | Industrielle Umgebungen oder Küstenregionen mit mäßigem Salzgehalt. | Chemieproduktion, Schwimmbäder, Boote und Küstenwerften. |
C5 I (Industrie) – sehr hoch | Industrielle Umgebungen mit hoher Luftfeuchtigkeit und aggressiven Atmosphären. | Gebäude mit fast ständiger Kondensation und hoher Verschmutzung. |
C5 M (Marin) – sehr hoch. NORSOK M501 entspricht dieser Klassifizierung. | Küsten- oder Offshore-Gebiete mit hohem Salzgehalt. | Gebäude mit fast ständiger Kondensation und hoher Verschmutzung. |
Wie oft wird gewartet?
Neben den Umweltfaktoren spielt bei der Auswahl des Oberflächenschutzes ebenfalls die vorgesehene Häufigkeit der Wartung der gegebenen Konstruktion eine große Rolle. Eine schwer zugängliche Konstruktion, wie etwa eine auf dem offenen Meer stehende Windkraftanlage mit wenigen Wartungsintervallen, wird wahrscheinlich einen anderen Schutzgrad erfordern als eine Industriepumpe, die unter milden Bedingungen arbeitet und einfacher gewartet werden kann.
Die Norm ISO 12944 gibt Aufschluss über den Haltbarkeitsgrad, die die Oberflächenbehandlung gemäß den folgenden Wartungsintervallen einhalten muss:
- Niedrig: 2 bis 5 Jahre
- Mittel: 5 bis 15 Jahre
- Hoch: mehr als 15 Jahre
Der erforderliche Schutzgrad kann auf Basis der Einflussfaktoren der Umgebung und dem Wartungsintervall für eine gegebene Konstruktion berechnet werden. So sollte beispielsweise eine Offshore-Anwendung im Freien mit einem Wartungsintervall von 10 Jahren das Schutzniveau C5-M erfüllen können.
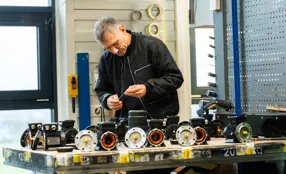
Die Beschichtungsdicke ist nicht alles
Die auf dem Markt erhältlichen Systeme zum Oberflächenbehandlung bestehen aus präzise komponierten Grundierungs-, Zwischen- und Deckschichten. Das gleiche Schutzniveau kann auf unterschiedliche Weise erreicht werden, und es erfordert Fachkenntnisse in Sachen Technik und Chemie, um den optimalen Schutz zu erzielen.
Dies bedeutet, dass die Zusammensetzung der Beschichtung von Hersteller zu Hersteller sehr unterschiedlich sein kann, je nach Stärke der Grundierung und der verschiedenen Beschichtungen. Mit anderen Worten, es reicht nicht aus, nur zu sagen, dass die Oberflächenbehandlung eine bestimmte Dicke haben muss, da dies kein klares Bild davon vermittelt, ob die Behandlung die Schutzanforderungen erfüllt.
Weitere Optionen
Im Zusammenhang mit den verschiedenen Zusatzanforderungen, die an die Oberflächenbehandlung gestellt werden, ist in der Regel die Wahl verschiedener Optionen möglich, wie etwa:
- Berichte über die Oberflächenbehandlung
- FROSIO-Beschichtungsinspektionen
- Messung der Stärke der Beschichtung
- Untersuchung der Widerstandsfähigkeit der Oberflächenbehandlung gegen verschiedene Faktoren und Umgebungsbedingungen